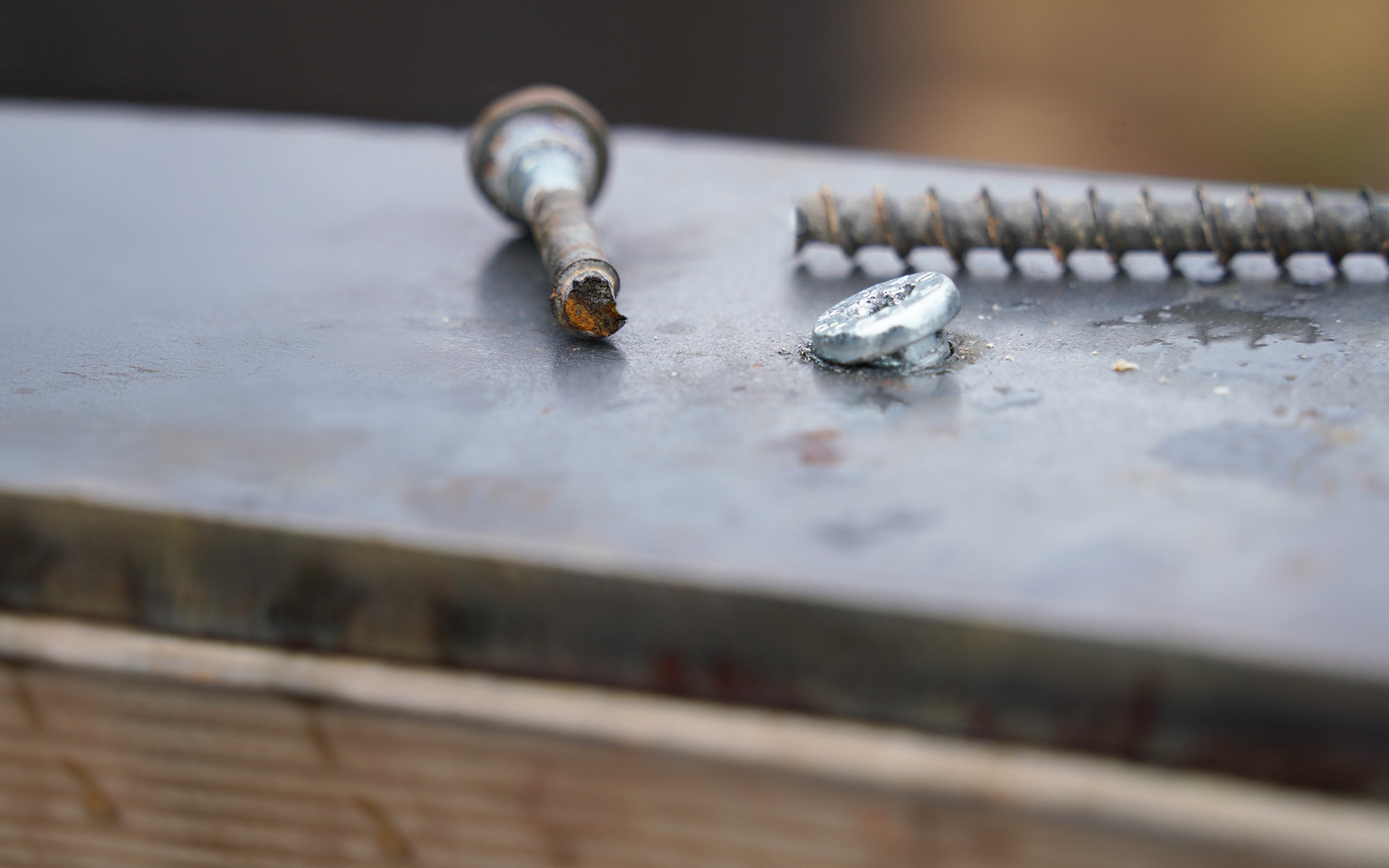
Understanding the challenge of premature failure
Timber screw failure, although rare, can occur, particularly in more demanding environments and applications.
These isolated cases – premature failure is observed in approximately 1 project out of 1000 – are predominantly found in metal-to-timber connections, where conditions are the most demanding.
Precisely because of their infrequency, for years it has been challenging to identify a common denominator across all cases. However, the industry, together with engineers, builders and standardisation bodies, is now beginning to understand and address the factors contributing to these issues.
Modern large-scale timber buildings require high-performance screws to maximise the efficiency of complex connections, ensuring strength and reliability even under significant and sustained stress over time.
Achieving this level of performance, particularly for high-strength screws, requires attention to design, installation practices and environmental conditions, especially those related to humidity.
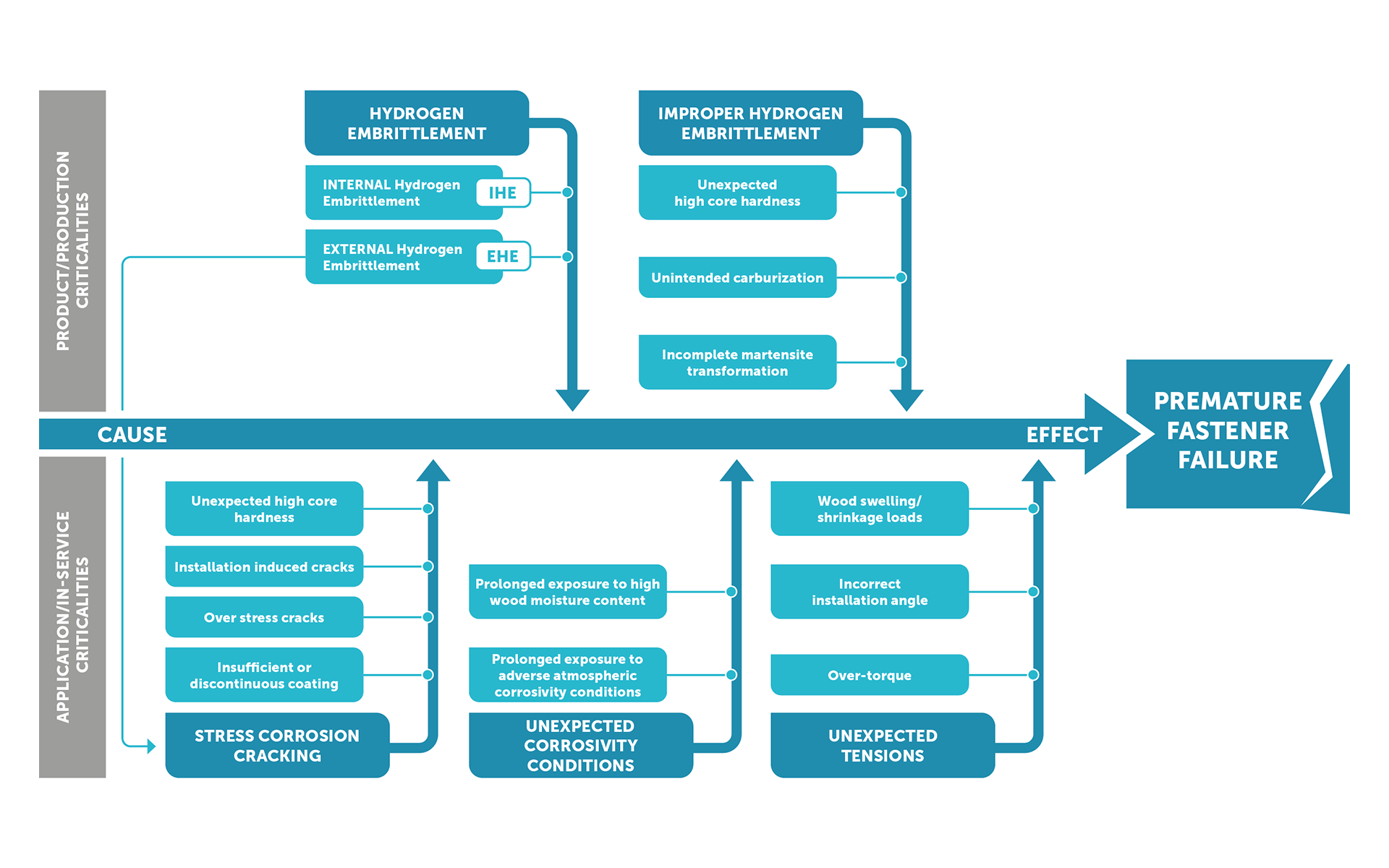
What Hydrogen Embrittlement is, and how it can damage screws
Hydrogen Embrittlement (HE) is a phenomenon where the absorption of hydrogen atoms into metallic materials, particularly high-strength steels, compromises screw performance by reducing their ductility and capacity. This makes screws more brittle and susceptible to premature failure under stress.
For Hydrogen Embrittlement to occur, three key conditions must be simultaneously met:
Presence of hydrogen,
Sustained load,
Material susceptibility.
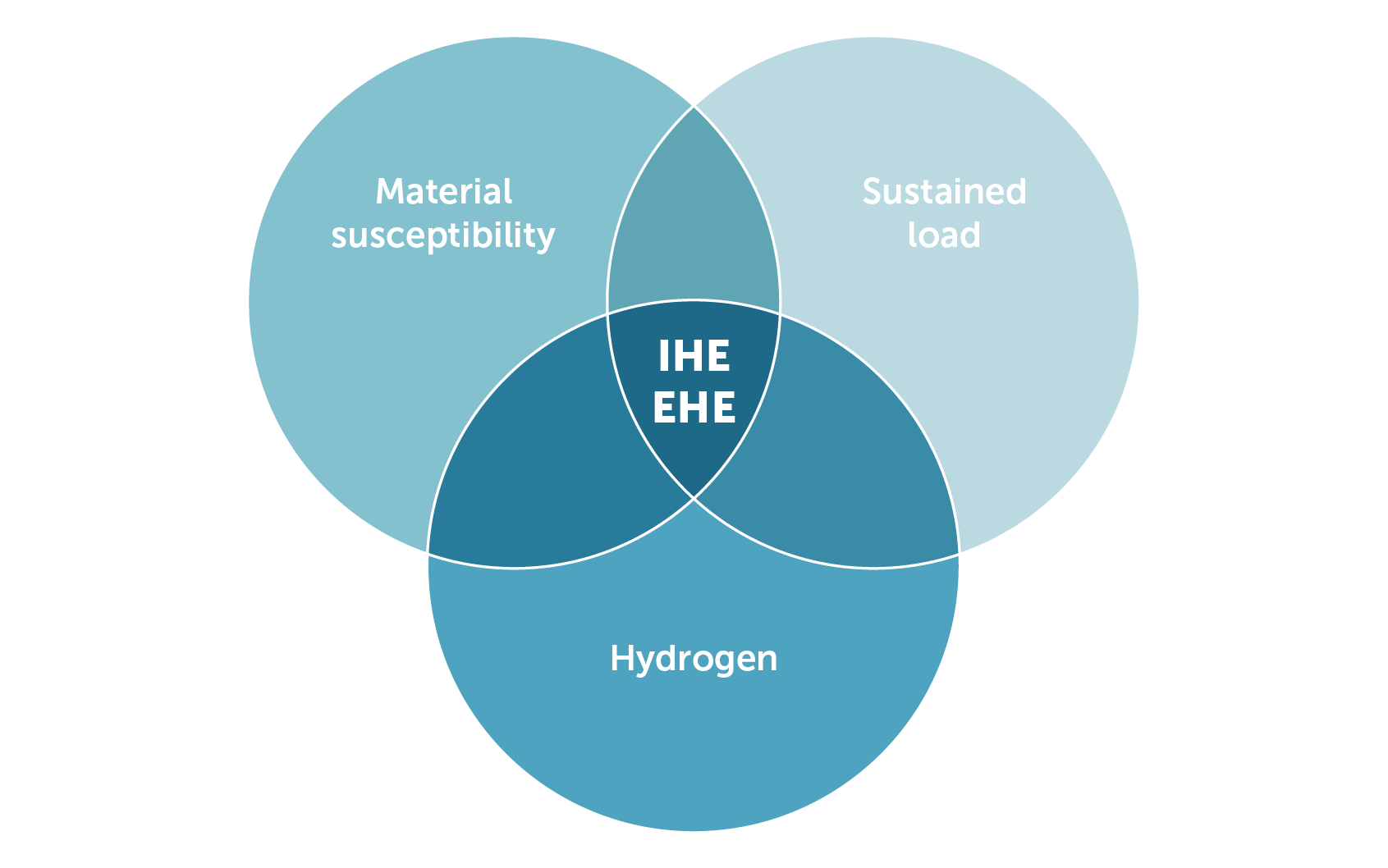
Primary causes of hydrogen-induced failure: the two types of Hydrogen Embrittlement
There are two types of Hydrogen Embrittlement, essentially differentiated by the timing of hydrogen absorption: either during manufacture or after the fastener has been installed.
Internal Hydrogen Embrittlement (IHE): occurs during manufacturing processes, such as pickling or electrolytic zinc plating, where hydrogen atoms infiltrate the screw’s microstructure and become trapped.
Environmental Hydrogen Embrittlement (EHE): occurs during the product's service life, when screws absorb hydrogen from external sources, particularly in humid environments, primarily due to corrosion.

Internal Hydrogen Embrittlement – IHE:
During manufacture, certain processes expose screws to environments conducive to hydrogen absorption. As a result, atomic hydrogen forms on the metal surface and diffuses into the steel.
The most influential processes are pickling, followed by electrolytic zinc plating, while heat treatment plays a relatively minor role in the context of timber screws.
Acidic solutions used in pickling generate hydrogen as a by-product, which then diffuses into the screw material. This process is the main contributor to hydrogen absorption during manufacture, particularly in high-strength screws, whose microstructure retains hydrogen more effectively.
During electrolytic zinc plating, hydrogen is generated on the screw’s surface and can diffuse into the material.
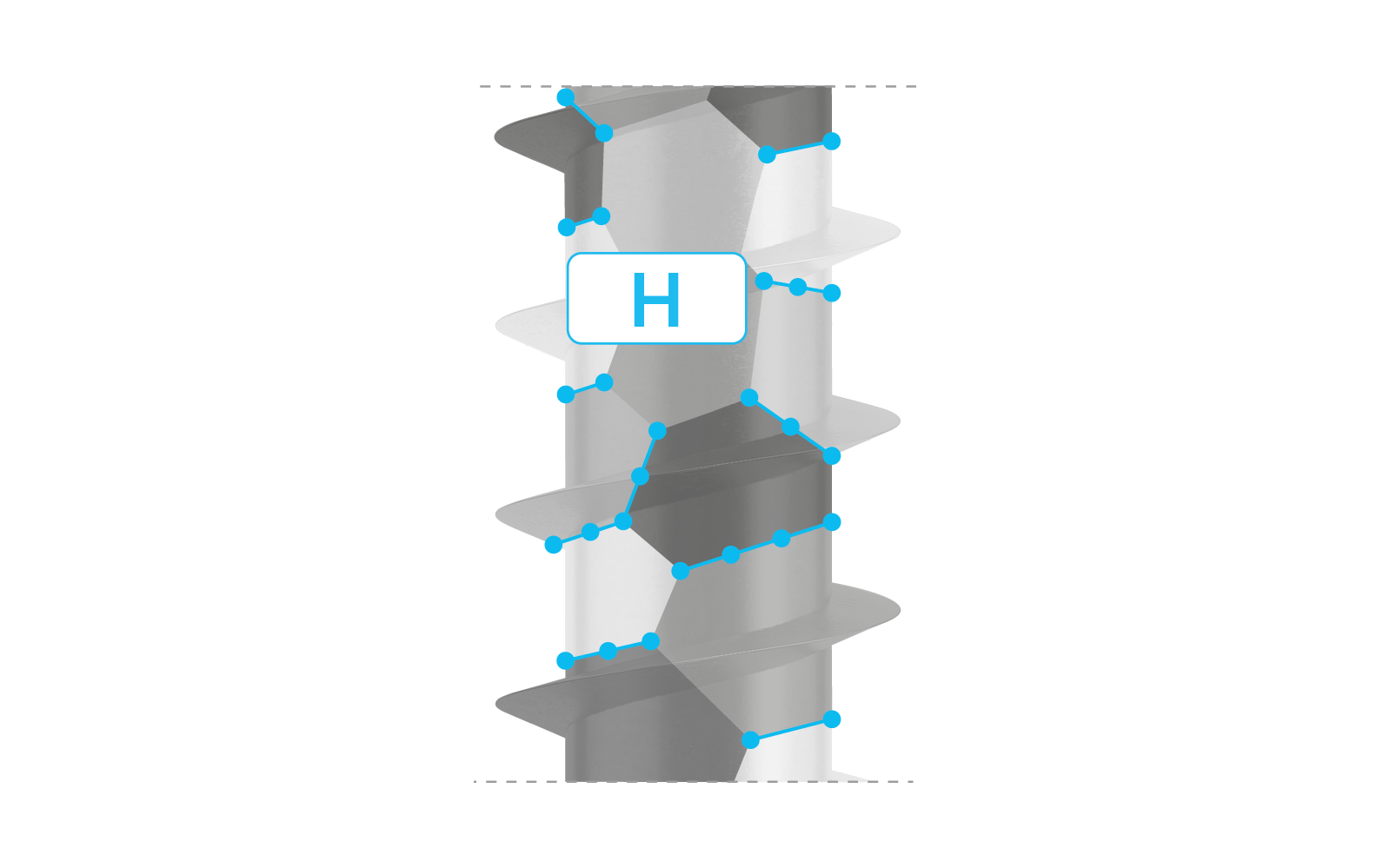
Rothoblaas screw manufacturing processes incorporate advanced measures to minimise the risk of hydrogen absorption:
Optimisation of heat treatment cycles to promote hydrogen diffusion before cooling.
Use of inhibitors in pickling baths to suppress hydrogen generation.
Post-zinc plating treatments for dehydrogenation at 150–200°C for longer screws.
Storage of screws in dry, controlled environments to preserve their integrity.
Although these measures represent industry standards, Rothoblaas ensures their consistent application across all manufacturing facilities. Moreover, specific tests for Hydrogen Embrittlement, conducted in accordance with ISO 15330, are an essential part of our Quality Control. These tests guarantee compliance with safety standards by assessing the mechanical performance of fasteners from various production batches.
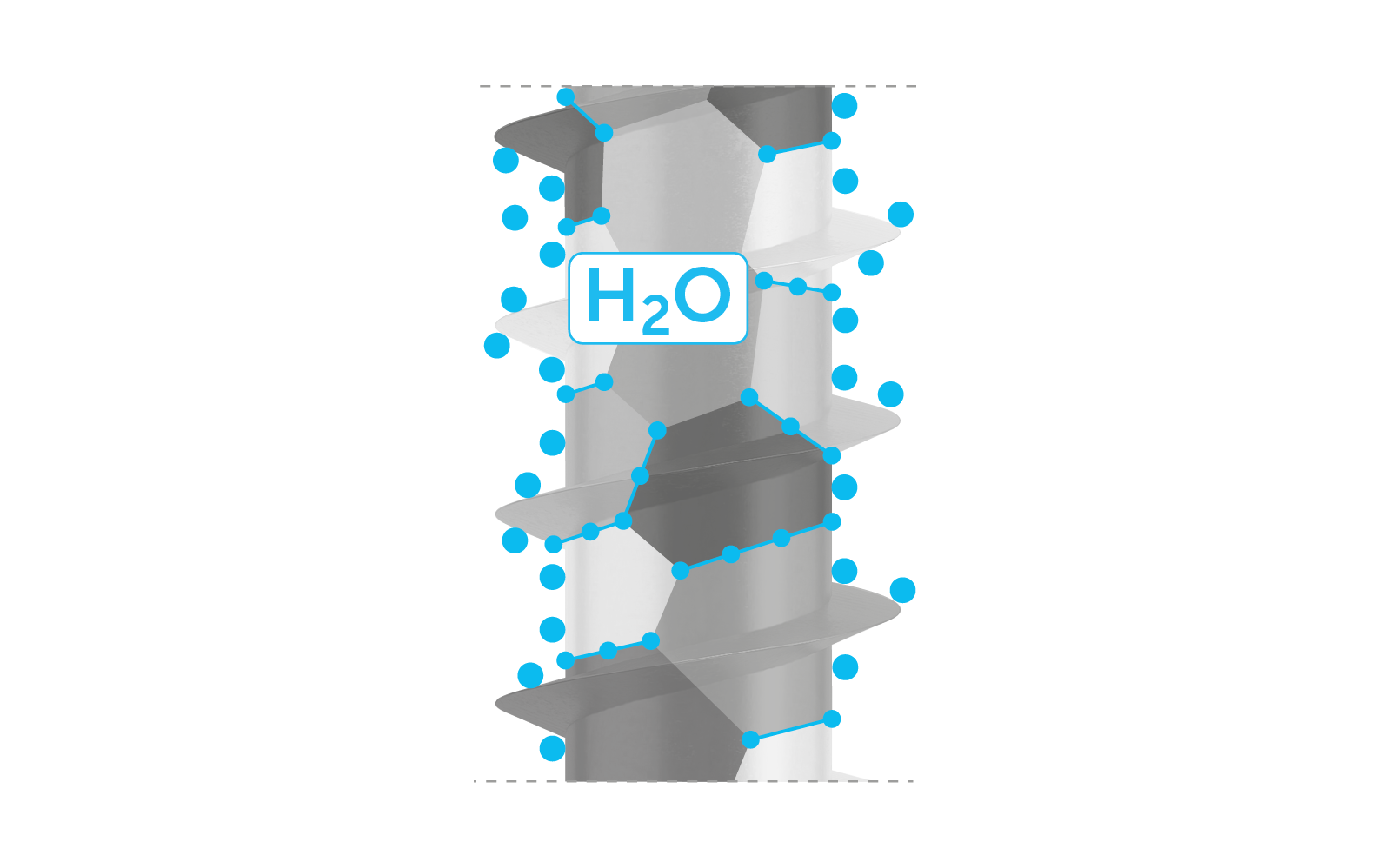
Environmental or External Hydrogen Embrittlement - EHE
In EHE, hydrogen atoms diffuse from the outside into the crystalline structure of the metal, accumulating at grain boundaries, inclusions or dislocations.
Corrosion is the primary factor generating hydrogen on metal surfaces, occurring through electrochemical reactions in the presence of water, particularly in acidic or chloride-rich conditions.
The hydrogen produced by these reactions permeates the metal, and in the presence of microcracks, can accumulate at the tips, promoting their propagation and triggering the embrittlement process. This localised weakening is further exacerbated by the formation of corrosion pits and rust layers, which facilitate hydrogen absorption, particularly during cyclical alternation between wet and dry conditions.
Given the impact of corrosion, moisture plays a crucial role in Environmental Hydrogen Embrittlement (EHE), as its presence is directly linked to the corrosiveness of wood environments in particular, as described in the wood corrosivity classes outlined in EN 14592:2022 (see Rothoblaas Smartbook).
How Environmental Hydrogen Embrittlement (EHE) occurs: stages of hydrogen absorption
Hydrogen absorption primarily occurs in two critical stages:
1) Exposure during construction: during the construction of buildings, before the structure is enclosed, fasteners are often exposed to significant ambient humidity.
Stagnant water, prolonged exposure to rain, or condensation can accelerate corrosion, facilitating the penetration of hydrogen into the screws.
The use of temporary protections, such as membranes, sealants, tarps or coverings, and maintaining as dry conditions as possible in the connections, is essential in minimising risks during this stage.
In the event of uncertainty regarding moisture conditions or where high humidity and limited protection are anticipated, it is recommended to select materials or coatings for screws with advanced corrosion resistance.
2) Service conditions: during the design stage, if connections are expected to face high or uncertain levels of humidity – such as in borderline Service Class 2 scenarios – a cautious approach is essential.
One applicable measure is to treat the connection as part of a higher service class than the one designated for the entire structure, thus accounting for long-term risks.
This choice involves applying higher safety factors and selecting advanced coatings or corrosion-resistant materials accordingly.
Ensuring appropriate long-term protection, such as using membranes, sealants and other permanent protective systems, remains crucial in safeguarding the durability and reliability of the connection.
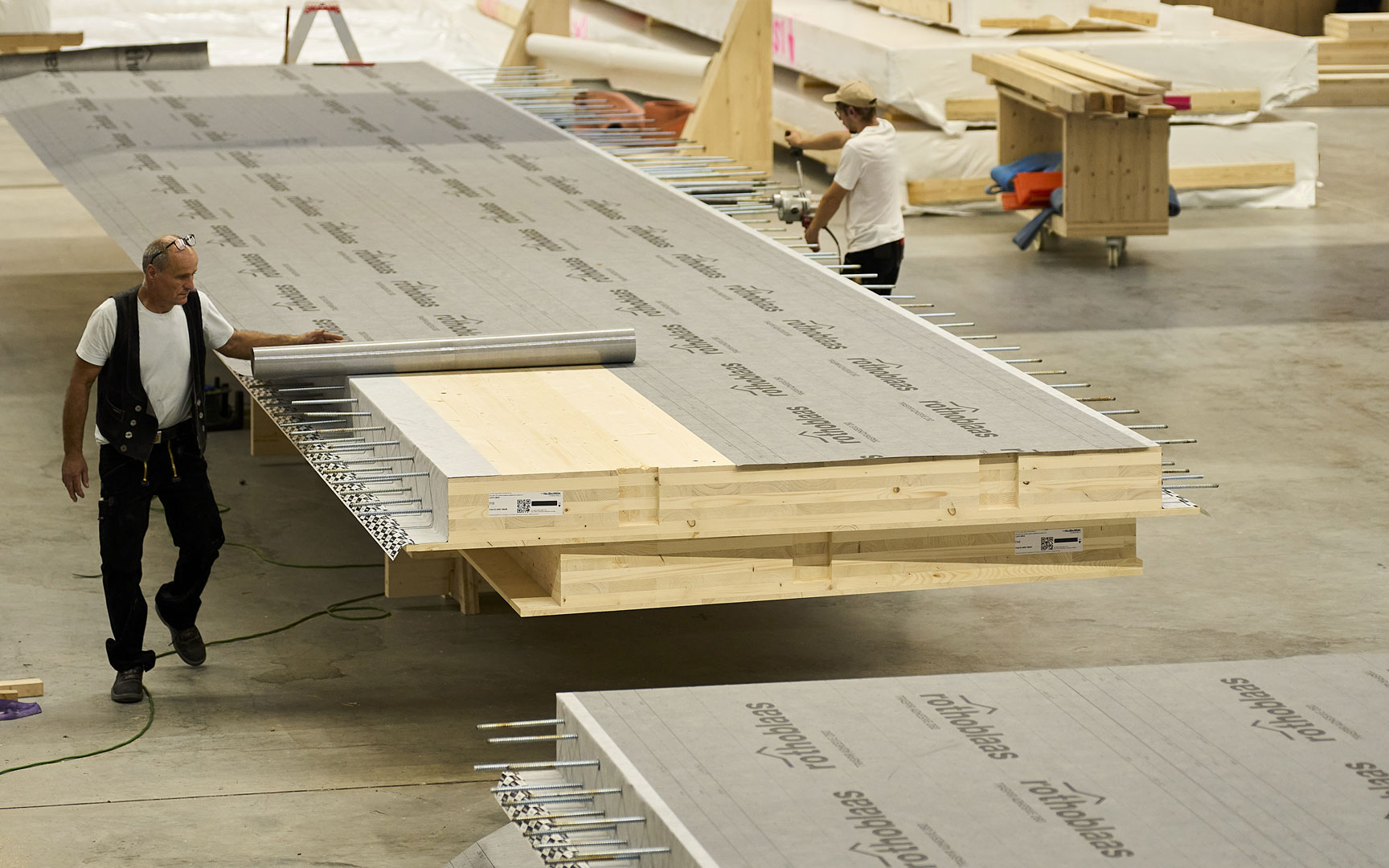
Techniques to prevent hydrogen-induced fractures: material selection based on environmental exposure
The choice of screw material and coating requires careful consideration of the corrosive conditions that the connection will face during construction and the entire service life of the building.
The checklist of factors to consider when making the selection includes:
Wood corrosivity: since the primary reactions occur within the timber, the wood corrosivity class (T1 to T5, as defined by EN 14592:2022) plays a critical role in Hydrogen Embrittlement, representing the most significant factor to assess.

Atmospheric corrosion: the corrosion of the exposed portion of the screw also plays a significant role in EHE, though it is generally less critical than the corrosivity of the timber itself.
Environmental factors, such as the presence of chlorides derived from sea spray – common in coastal construction sites and prefabricated elements transported by sea – or chlorine in swimming pools, accelerate the corrosion process.
Moreover, water can become trapped beneath the steel plates, increasing the local moisture content in the timber and concentrating corrosive agents around the fastener, further aggravating the risk of corrosion and subsequent Hydrogen Embrittlement.
Selecting the appropriate material and coating for specific conditions is as crucial as thoroughly evaluating the exposure environment. Implementing a moisture management plan is thus a particularly useful measure for mitigating risks.
Even with the proper choice of material and coating, improper installation of fasteners or unintentional sustained loads can damage or compromise the coating, promoting corrosion and enabling EHE.
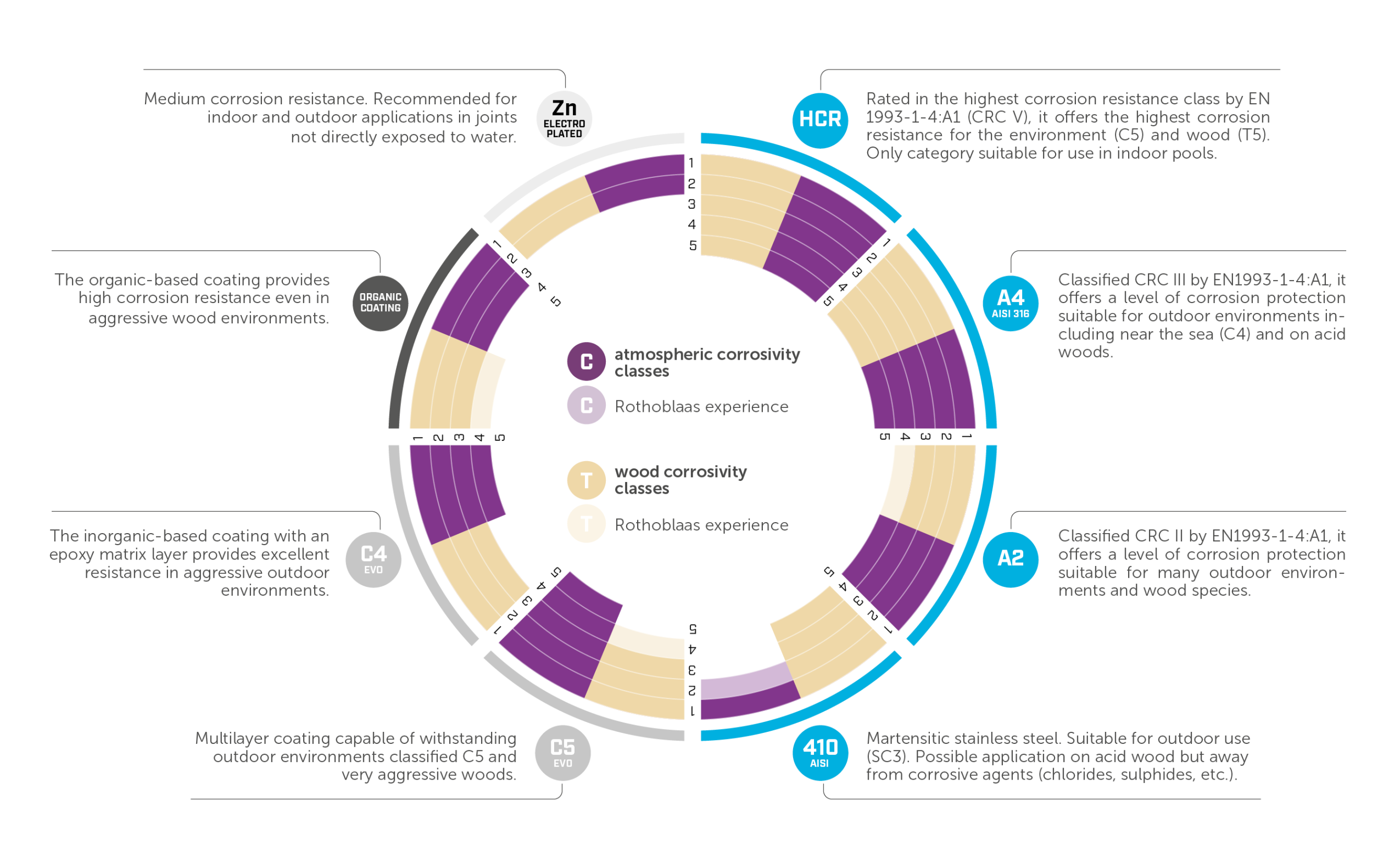
Unintentional sustained stress: stress factors that intensify hydrogen diffusion
While loads resulting from tensile forces are a natural condition for screws in structural applications, unintentional stress factors can significantly increase the risk of failure.
These stress factors overload the screw and create conditions that may lead to failure, even in the absence of Hydrogen Embrittlement (HE).
When combined with HE, they intensify hydrogen diffusion and material weakening, accelerating premature failure.
This occurs because the applied loads allow hydrogen atoms to migrate towards points of high stress concentration, such as microcracks, grain boundaries or the fillet radius under the screw head. The accumulation of hydrogen at these sites weakens the material's microstructure and triggers the formation of cracks, which can propagate and result in failure.
To mitigate the risks of premature failure, it is essential to identify and control the main sources of unintentional stress, particularly during installation.
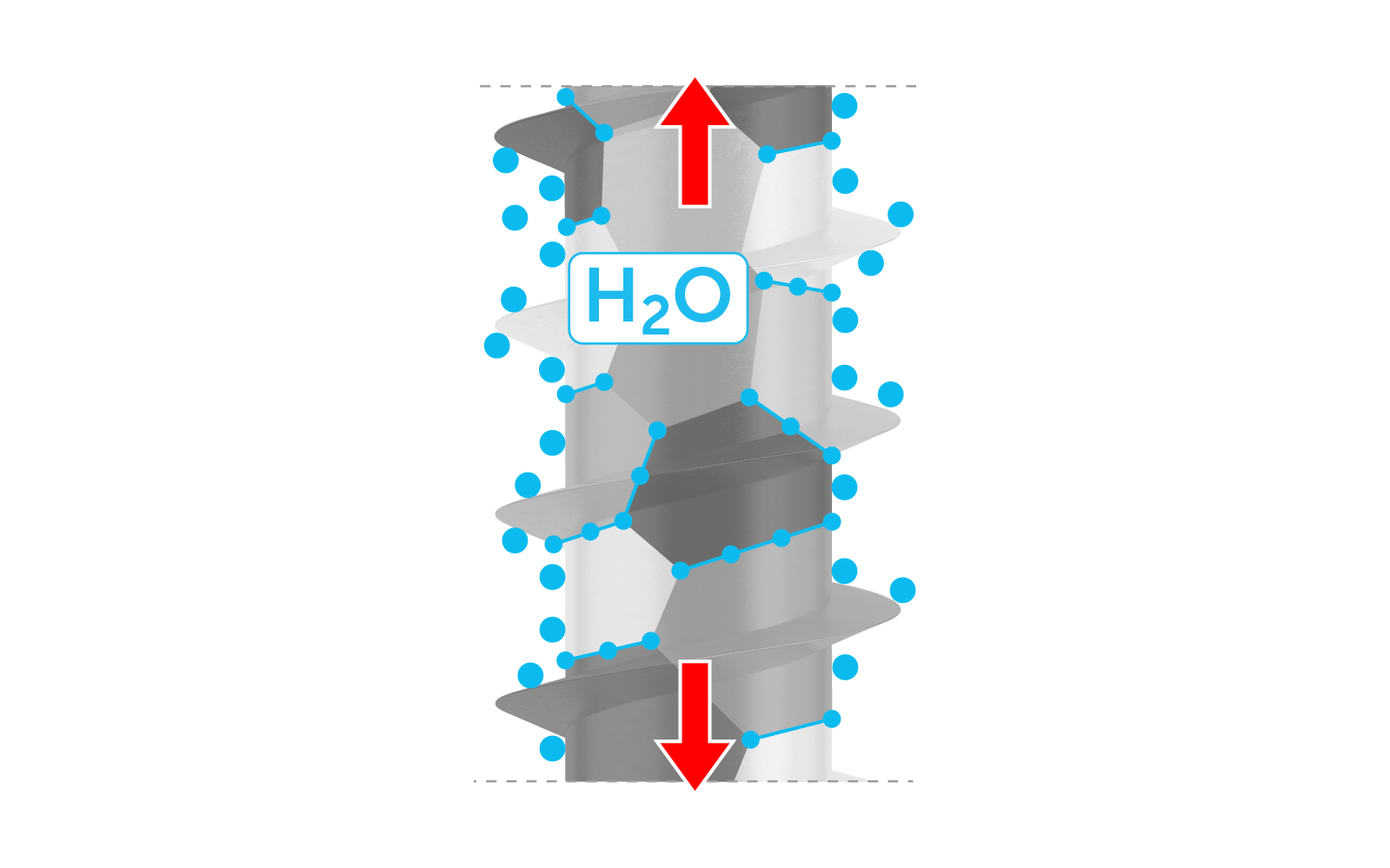
What are the possible sources of unintentional stress?
1) Installation torque: each type of screw has a defined torque range for proper installation, with a minimum torque to ensure full tightening and a maximum torque beyond which the screw’s integrity may be compromised. Exceeding this limit – over-torquing – adds stress factors to the screw that can accumulate and lead to premature failure.
Over-torquing alone can cause screw failure, even in the absence of Hydrogen Embrittlement, and may damage protective coatings, especially in steel-to-timber connections.
The application of excessive forces under the screw head or along the thread can strip the coating, exposing the screw to corrosive elements and increasing the risk of EHE.
Impact and percussion screwdrivers can generate very high torque, increasing the likelihood of overtorque. These tools, although efficient, lack the necessary control to maintain proper torque during installation, especially in steel-to-timber applications. Rothoblaas explicitly recommends avoiding the use of percussion screwdrivers for steel-to-timber connections.
To mitigate the risk of overtorque:
Use torque control devices (such as TORQUE LIMITER)
Use templates to prevent misalignment and reduce the forces applied during installation.
2) Incorrect installation angles: misaligned screws create uneven load distributions, leading to stress concentrations at specific points that increase the fastener's vulnerability to fractures.
Even in materials with low susceptibility, any crack subjected to loads in a corrosive environment can propagate and cause failure due to EHE – a risk often preventable by implementing proper installation practices.
When an incorrect angle is combined with over-torquing, the screw could bend to align with the hole, forcing the head into full contact with the plate. This can result in:
Pretensioning
Bending
Coating damage, further compromising the screw's integrity.
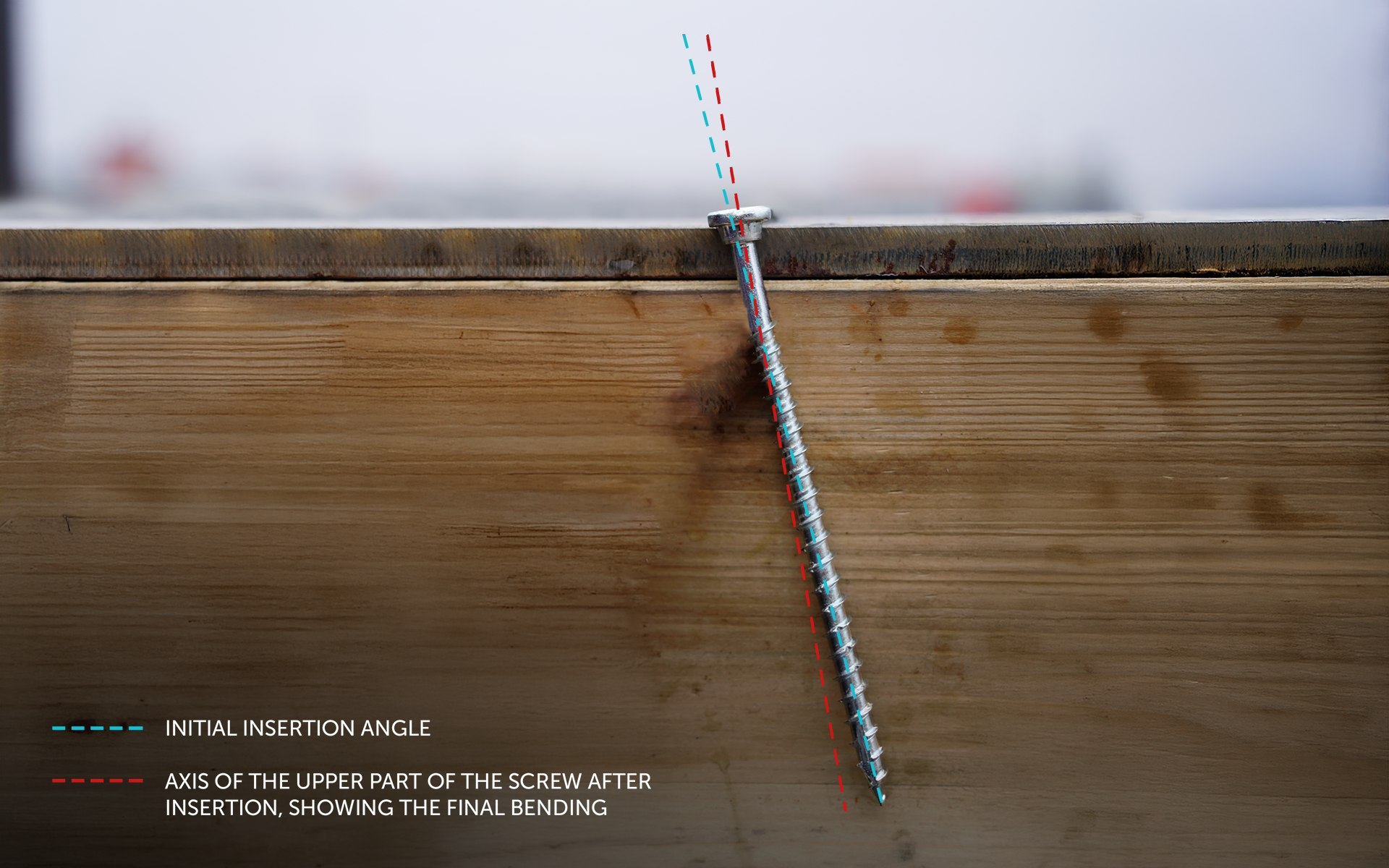
3) Timber swelling: timber is a dynamic material that responds to variations in ambient humidity by expanding and contracting. Swelling can exert considerable forces, particularly in steel-to-timber connections where the rigidity of the metal plate confines the timber, preventing it from deforming freely.
Research conducted by the University of Alberta and Rothoblaas shows that, compared to values measured under correct installation conditions, this induced tensile stress can be significant: the combination of over-torquing by two times greater than the recommended value and wood swelling can lead to a stress level of more than 65% of the screw's ultimate tensile capacity. (Ftens ≃ 0.65 ftens,k).

4) Connection stiffness: the stiffness of the connection also plays a role in the distribution and absorption of stress. Timber-to-timber connections with softwoods, being more flexible, allow for better energy dissipation, thus reducing stress concentration on the screws.
Connections involving engineered timber products, such as LVL and CLT, fall into an intermediate category insofar as naturally more rigid due to their higher density and structural composition compared to softwoods.
At the other end of the scale, we find steel-to-timber connections, especially those involving thick steel plates, which are significantly more rigid.
Under high-stiffness conditions, unintentional stress can be more intensely concentrated on the screws.
Overtorque further increases the connection's stiffness, making it more vulnerable to stresses induced by timber swelling and, consequently, to failure.
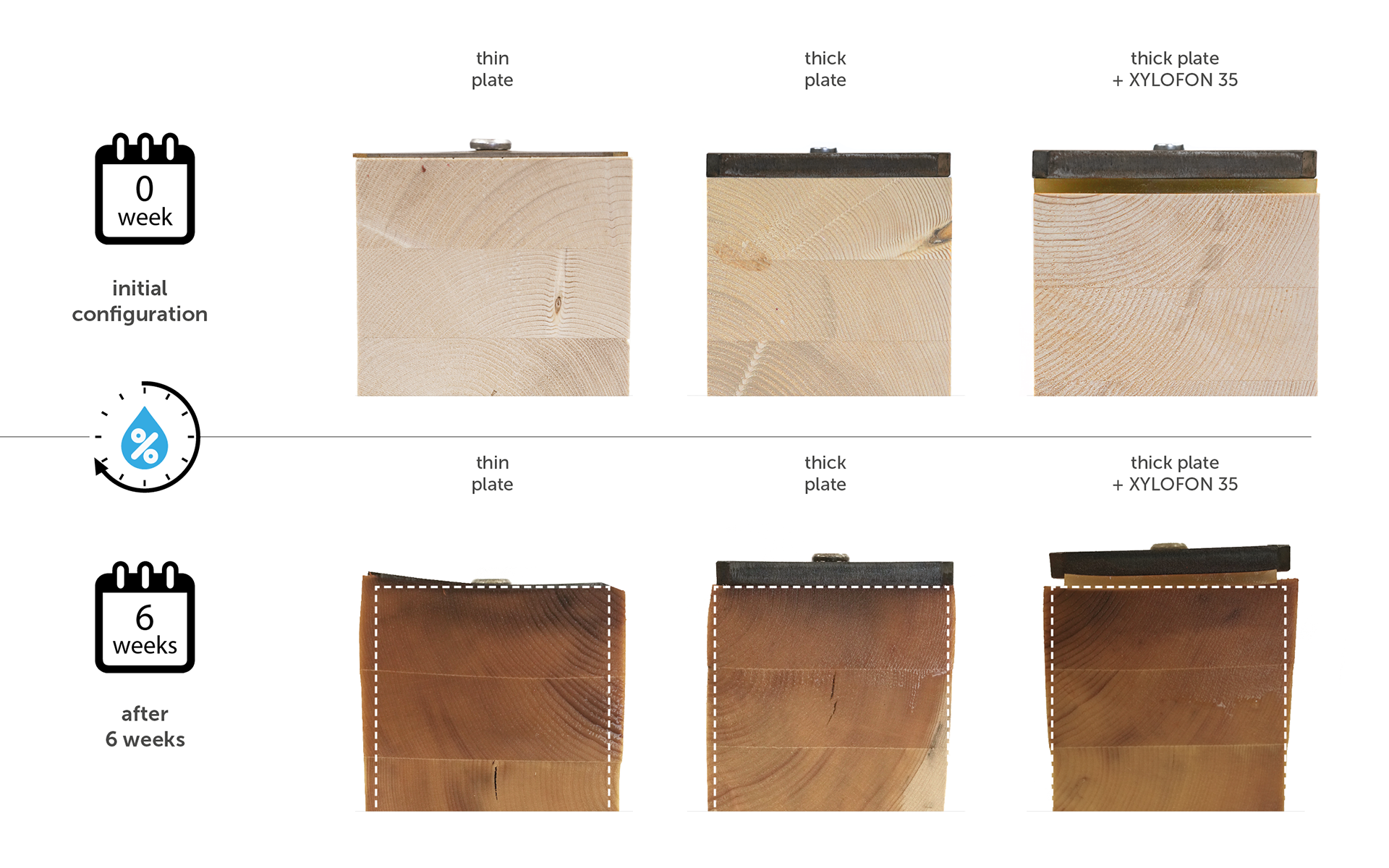
Incorporating design considerations that account for all these factors can mitigate the risk of premature failure, whether due to Hydrogen Embrittlement or other load-induced stresses. Essentially:
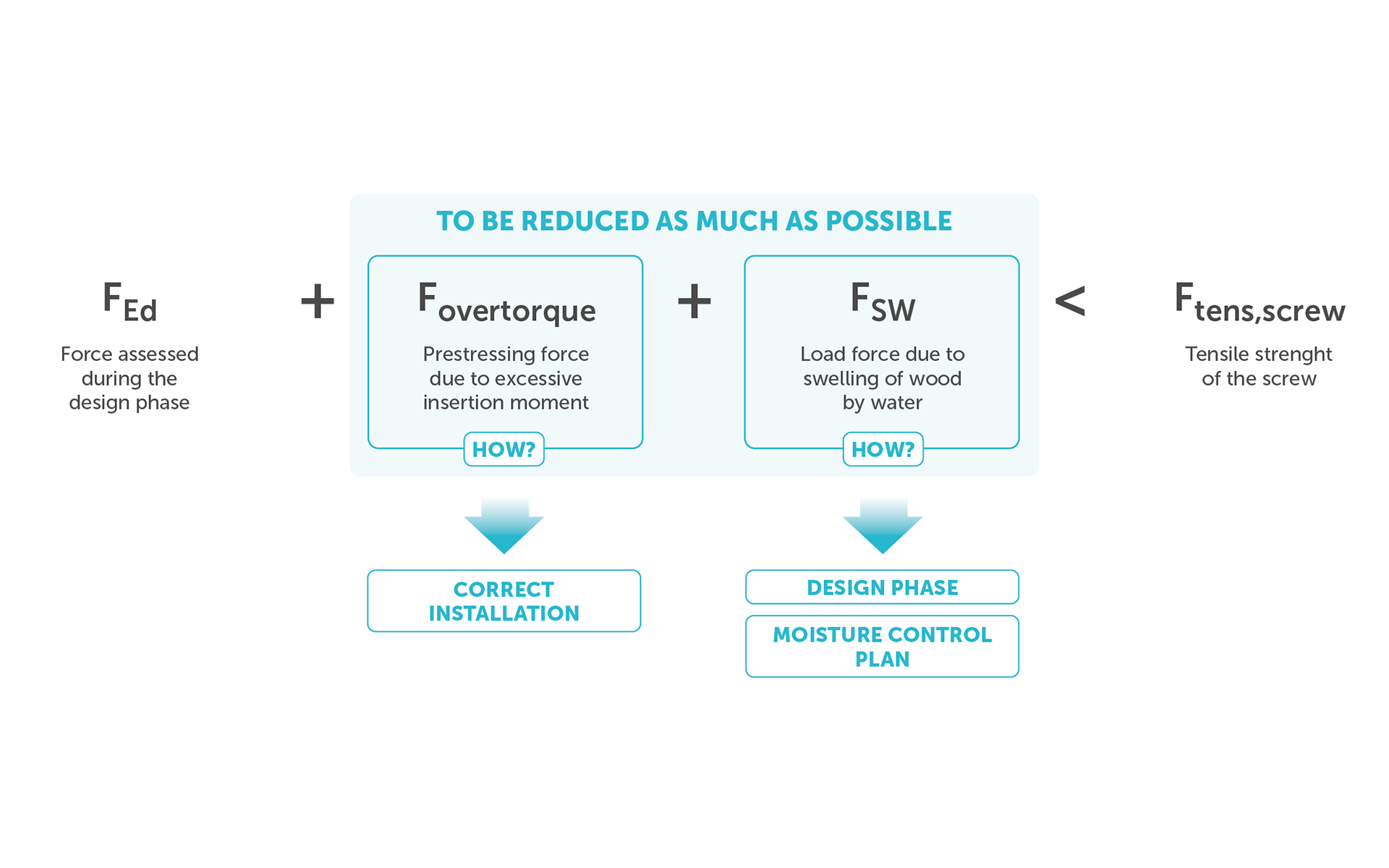
Susceptibility to Hydrogen Embrittlement: the role of core hardness
As material strength increases to meet tensile load requirements, the steel becomes harder, less ductile and more prone to hydrogen-related damage.
The risk of failure is particularly relevant for fasteners with high core hardness when exposed to unintentional stress and hydrogen sources.
Hardness thresholds
The core hardness threshold above which fasteners are considered susceptible to Hydrogen Embrittlement is generally set at 360 HV (Vickers Hardness), according to the following scale:
Below 360 HV: the risk of failure related to Hydrogen Embrittlement is minimal (though not completely eliminated), regardless of the application conditions.
Between 360 HV and 390 HV: the risk is considered manageable, provided the contributing factors are evaluated and mitigated.
Above 390 HV: susceptibility to Hydrogen Embrittlement increases significantly, requiring a thorough assessment of all other risk factors to ensure a safe and reliable connection.
Failure, whether dependent on Hydrogen Embrittlement or otherwise, can still occur even in fasteners with a core hardness below 360 HV. At the same time, using screws with a hardness exceeding 390 HV remains feasible if other contributing factors, such as moisture exposure and installation practices, are carefully evaluated and effectively managed.

Compliance: a global commitment
At Rothoblaas, providing products that meet the highest international standards for safety, performance, durability and compliance is a fundamental commitment.
Our structural screws are rigorously tested and evaluated to ensure reliability in timber connections worldwide, from Japan to Canada, making them among the most certified fastening solutions globally.
These certifications, issued by public and private entities, ensure adherence to stringent criteria through regular assessments and ongoing, periodic quality checks.
With this in mind, we aim to pioneer advancements aligned with CSA O86:2024, the world’s first timber construction standard regulating screw hardness requirements, marking an important step forward in addressing failure related to Hydrogen Embrittlement. Rothoblaas takes this regulation seriously and incorporates its principles into product development.
Rothoblaas fasteners are already designed and tested to meet the majority of globally recognised reference parameters:
ISO 2702 compliance: a standard focusing on hardness requirements to mitigate the risk of Environmental Hydrogen Embrittlement (EHE).
Hydrogen Embrittlement testing: conducted in accordance with ISO 15330,
Core hardness quality check: every production batch undergoes rigorous quality checks to ensure compliance with hardness thresholds. On request, screws can be manufactured to meet specific project requirements, such as 360 HV or 390 HV limits.
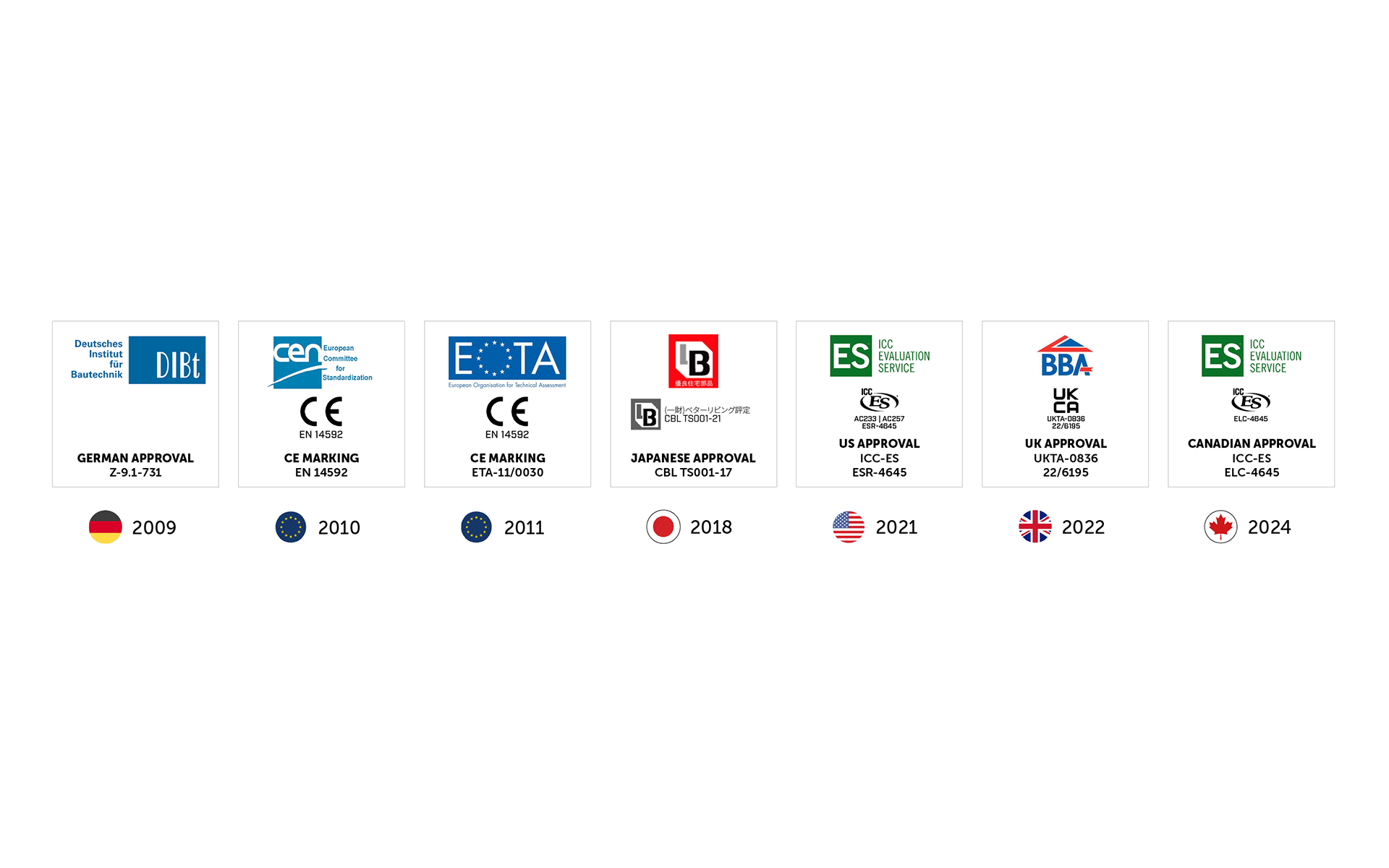
A shared responsibility for long-term success
Ensuring the reliability and safety of timber connections is a shared responsibility involving engineers, builders and manufacturers. Every stage requires a proactive approach, from selecting appropriate materials and coatings to implementing proper installation practices and moisture management strategies.
Using tools like a Risk Mitigation Matrix can provide a systematic approach to evaluating and addressing the key factors at play.
The key to mitigating the risks of premature failure lies in skilfully combining technological solutions, careful design and mindful installations. A safe present and future for timber buildings can only be achieved together.
All rights reserved
Technical Details
- Companies:
- any
- 国家:
- Any
- 产品:
- TORQUE LIMITER JIG VGU JIG VGZ 45° HBS PLATE VGS HBS PLATE EVO VGS EVO VGS A4 HBS PLATE A4